The controllers that are integrated in our automated screwdriving systems, are basically divided into screwdriving and process control systems. The screwdriving process controller monitors and controls the actual screwdriving process – it ensures that the preset speed, torque and depth are being maintained. In particular, the controller is important in evaluating the process and documentation of all screwdriving data. Process controllers are responsible for the control of the entire system. For example, they control the stroke movement of the screwdriving spindle, the feeding of fasteners or the communication with peripheral devices.
Control technology
Overview Control systems
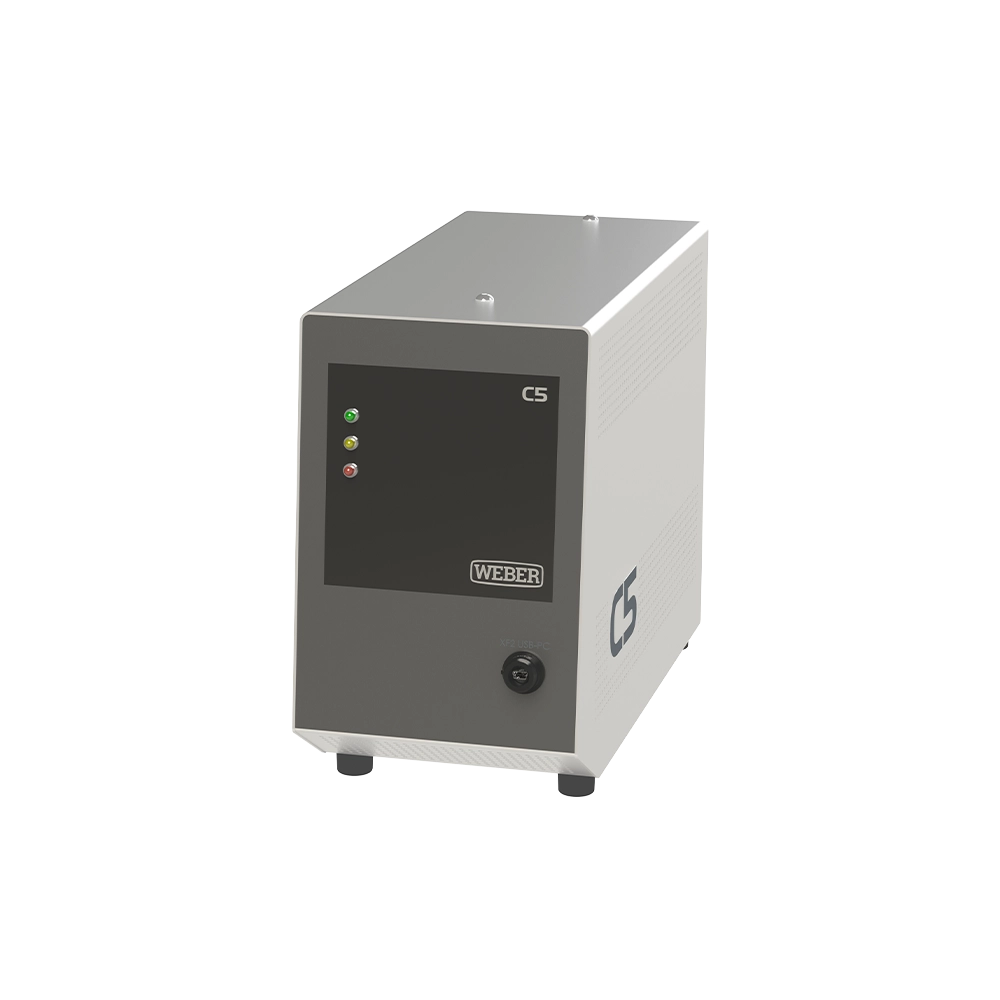
- Simple screwdriving tasks with easy parameterization
- Versatile screwdriving controller with good price-performance ratio
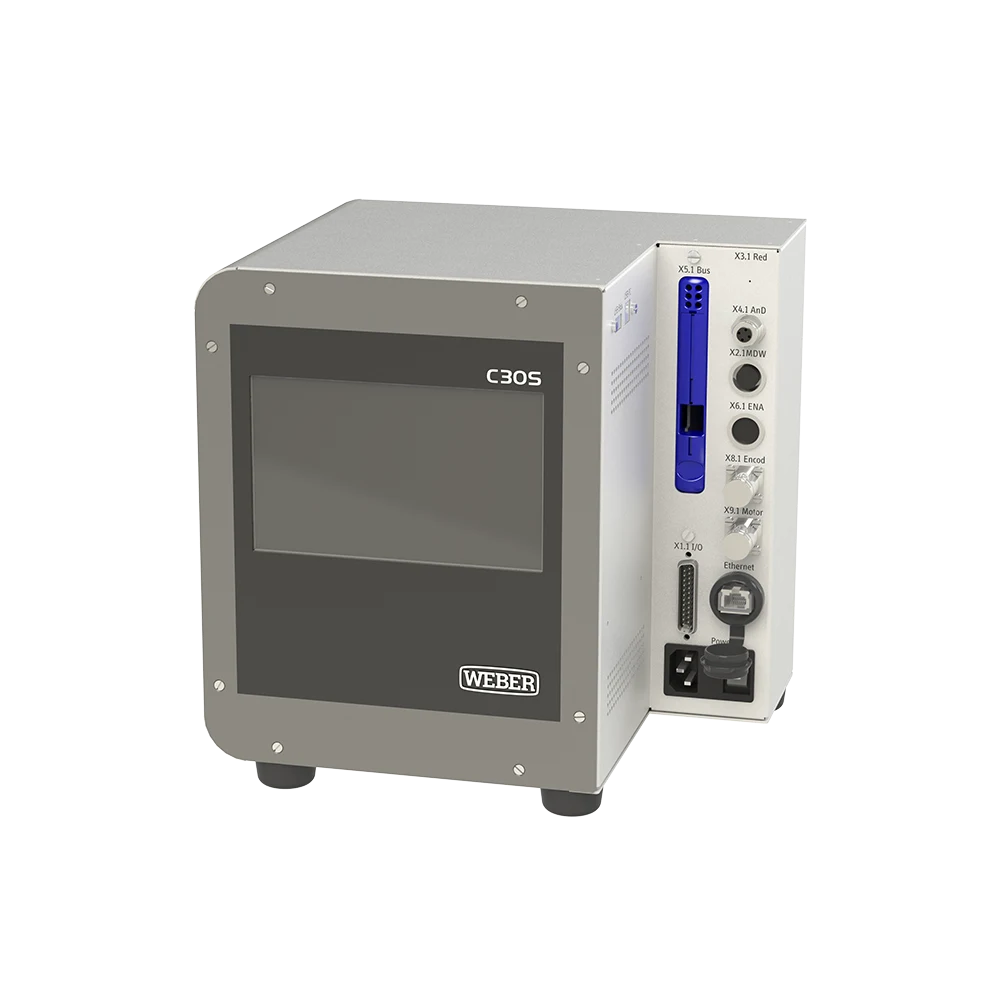
- Complex screwdriving tasks with simple parameterization
- Detailed evaluation and numerous interfaces
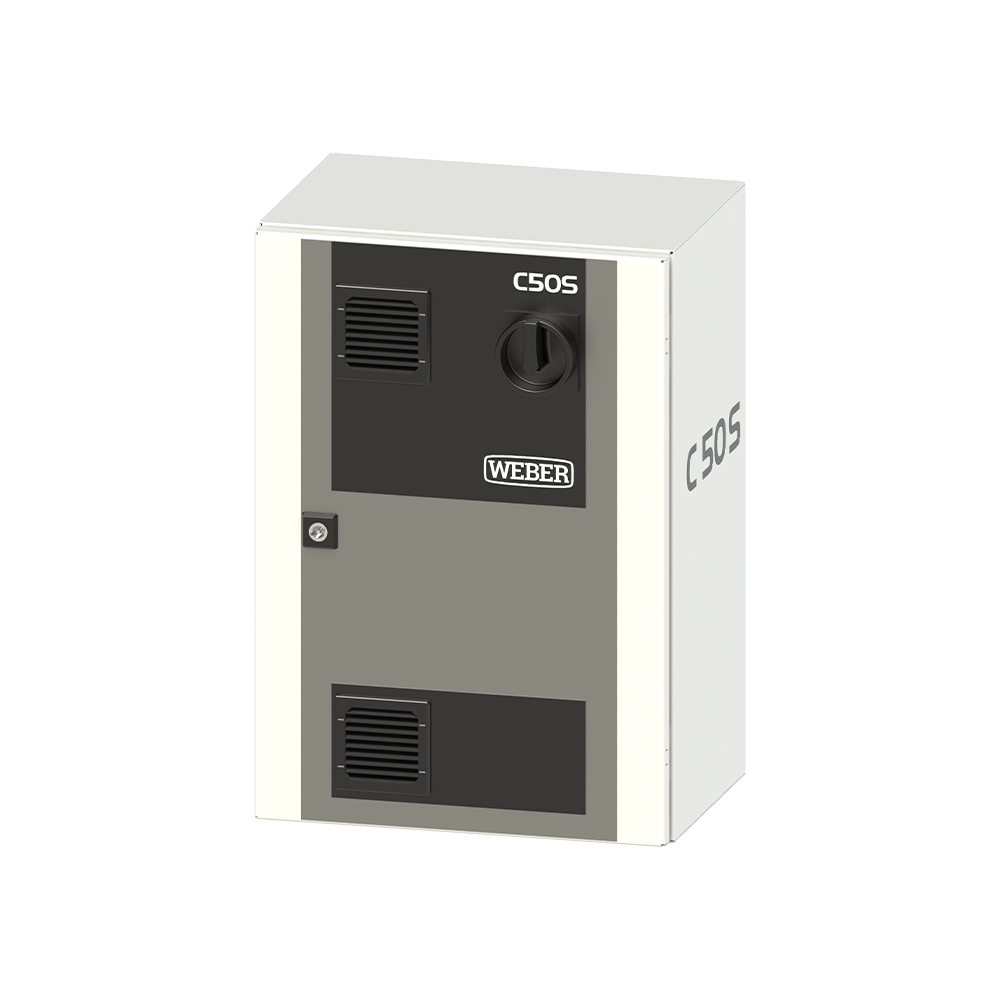
- Screwdriving process with flexible step programming
- Individual process flow configurable with latest methods
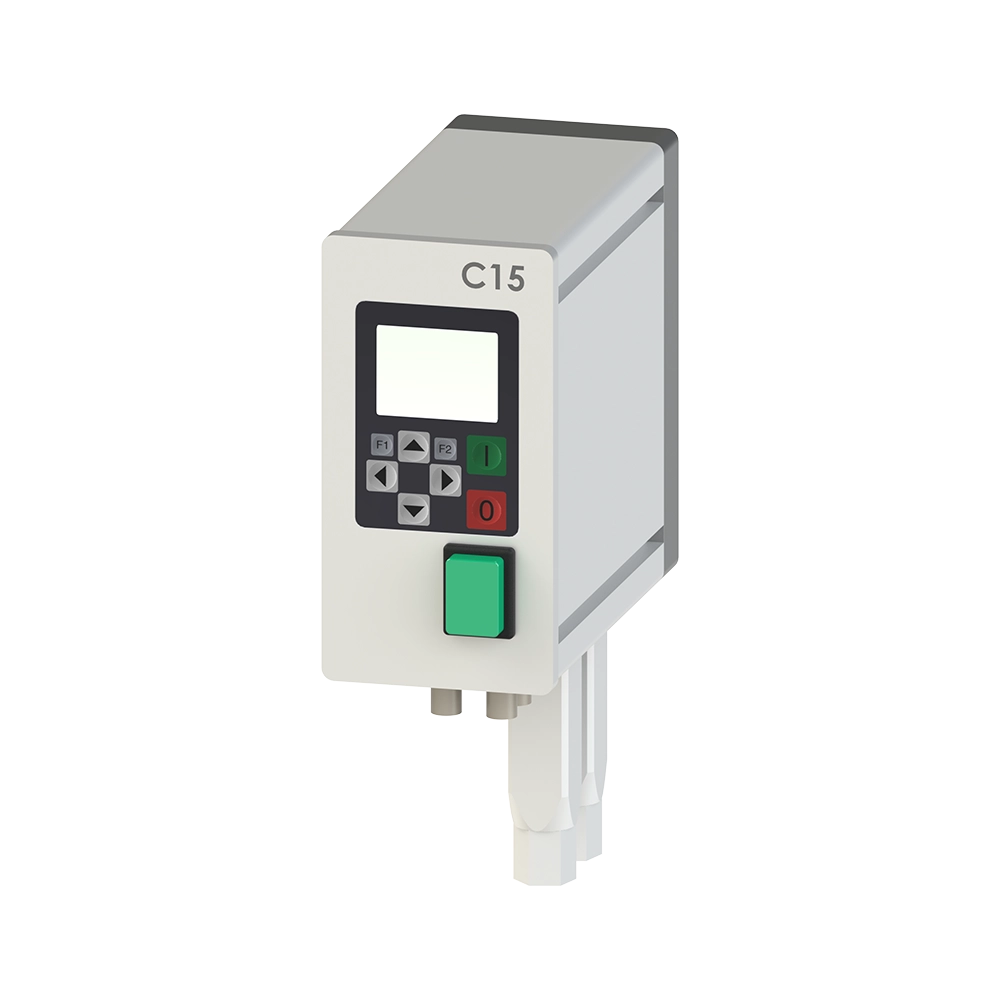
- C10S for pneumatic handheld screwdriving systems
- C15S for simple screwdriving systems
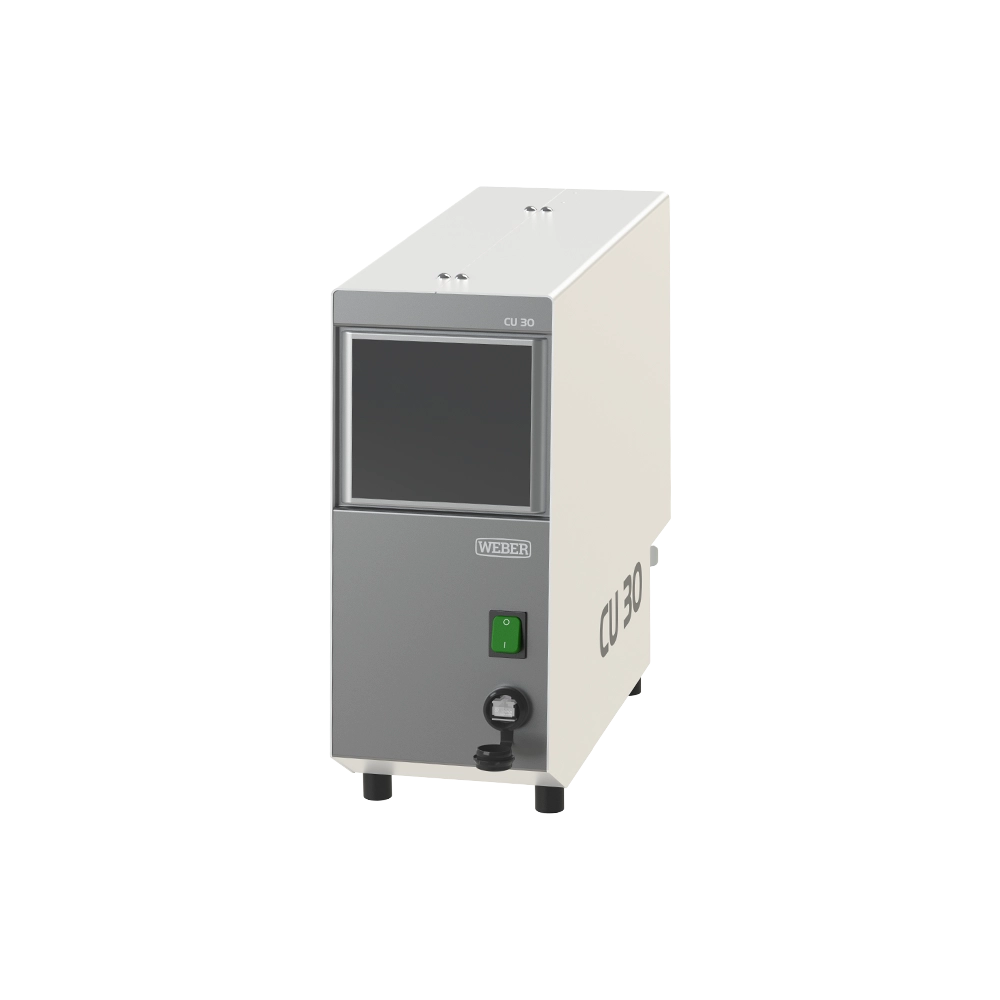
- PLC functionality with integrated pneumatics
- Simple handling through program modules and touch display
Further information on control systems
Process controller C5S
The process controller C5S is designed for simple screwdriving applications. It is used exclusively as a drive controller and is operated through a digital interface: switching the rotational direction and two speeds are possible.
Process controller C30S
The C30S was designed to solve complex tasks. Numerous open interfaces and screwdriving strategies make it a very versatile controller. Parameterization and operation take place via a 7-inch touch screen. The system is supplied as process controller C30SxS with current control and as model C30SxM with torque or rotational angle sensor.
Process controller C50S
The C50S controller for complex tightening tasks. Thanks to freely programmable screwdriving levels, every conceivable screwdriving application can be achieved reliably. Networking is realized via Ethernet with TCP/IP protocol. Parameterization, operation and visualization of the sequences are done through a computer with a Windows operating system.
Sequence controller C10 / C15
While the C10S serves as a pure feed controller for the pneumatic handheld screwdriver HSP, the C15 can also control fixtured screwdrivers with spindle functions. This is possible with depth and a torque shut-off via a torque clutch. The model C15 also has an open customer interface.
Sequence controller CU30
The sequence controller CU30 is used for handheld and fixtured screwdriving systems. Its extensibility ensures maximum performance thanks to the integrated PLC and pneumatics. The CU30 allows you to control almost all WEBER screwdriving systems, feed systems, press-fitting and insertion systems.
Frequently asked questions about the control of screwdriving and feeding technology!
How are individual products controlled from the customer side?
If our customers integrate screwdriving technology or individual components into their systems, they receive a function and pneumatics diagram so all essential interfaces of the respective product can be controlled with the customer control.
Can process parameters be stored, read out and visualized on the controller?
Screwdriving results can be stored and read out on the WEBER process controls C30S and C50S. The data are transferred over a bus system. The visualization is provided on an integrated 7” touch panel display on the C30S and on an external touch display on the C50S. The process data can also be exported into a MySQL database.
How can the screwdriving process be controlled?
The process control can monitor the screwdriving tasks using current, torque, angle, gradients and depth.
How is a sequence control different?
The sequence control is at a higher level than the process control and coordinates/controls the interaction of the sensors and actuators of the system (e.g. during feeding) as well as the process control.
Can the data be transferred to a higher-level control?
On the C30S or C50S for example, data can be transferred using a digital interface, Profibus, ProfiNet, Ethernet IP, Device NET and Ethernet CAT. The process data can also be exported into a MySQL database.
Which devices can be integrated into a fully automated screwdriving systems and controlled?
The hopper, feeder, distributor, brake and screwdriving or setting spindle can be integrated and controlled in a fully automated screwdriving system.
Is a stand-alone solution of WEBER screwdriving and feeding systems possible?
An independent workstation can be created by combining screwdriving or setting, feeding, process control and sequence control. The systems can be integrated into an existing workstation or supplied as a complete solution (screwdriving and assembly cell).
What is the function of a process control?
A process control – also referred to as a screwdriving controller – controls the drive of the screwdriving system. It can intervene in the screwdriving process using sensors (e.g. torque sensor or depth sensor) to ensure reliable connections).
WEBER Schraubautomaten
WEBER Schraubautomaten GmbH is a family-run and innovative company that attaches great importance to the sustainable design of the value chain. The result is high-quality products with maximum process reliability that make production processes more efficient. Your success is our success.