Everyone is talking about Industry 4.0. But what is it, exactly, in particular in the speciality field of screwdriving and feeding systems? The term “smart factory” is essential for this explanation. Smart factories are created by the digital linking of embedded production systems and dynamic engineering change processes. And that is precisely what Industry 4.0 is about: combining production and automation systems with modern information and communication technology. Digital processes provide employees of a Group of companies – including any worldwide operations – are provided with simpler and faster methods for communicating and evaluating data. Production, logistics and machine operation run more smoothly and with fewer faults
THE SIGNIFICANCE OF INDUSTRY 4.0
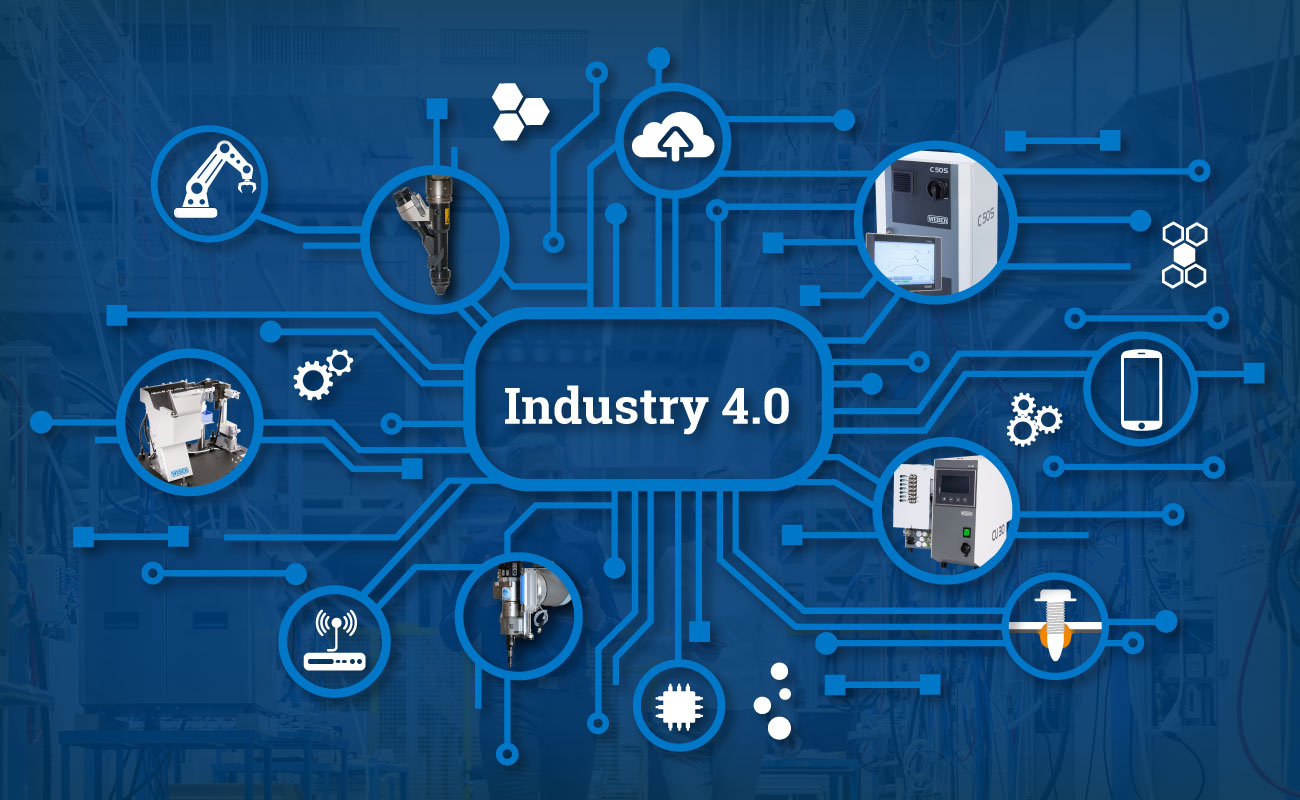
The significance of Industry 4.0 in screwdriving and feeding systems
How Industry 4.0 changes screwdriving and feeding systems
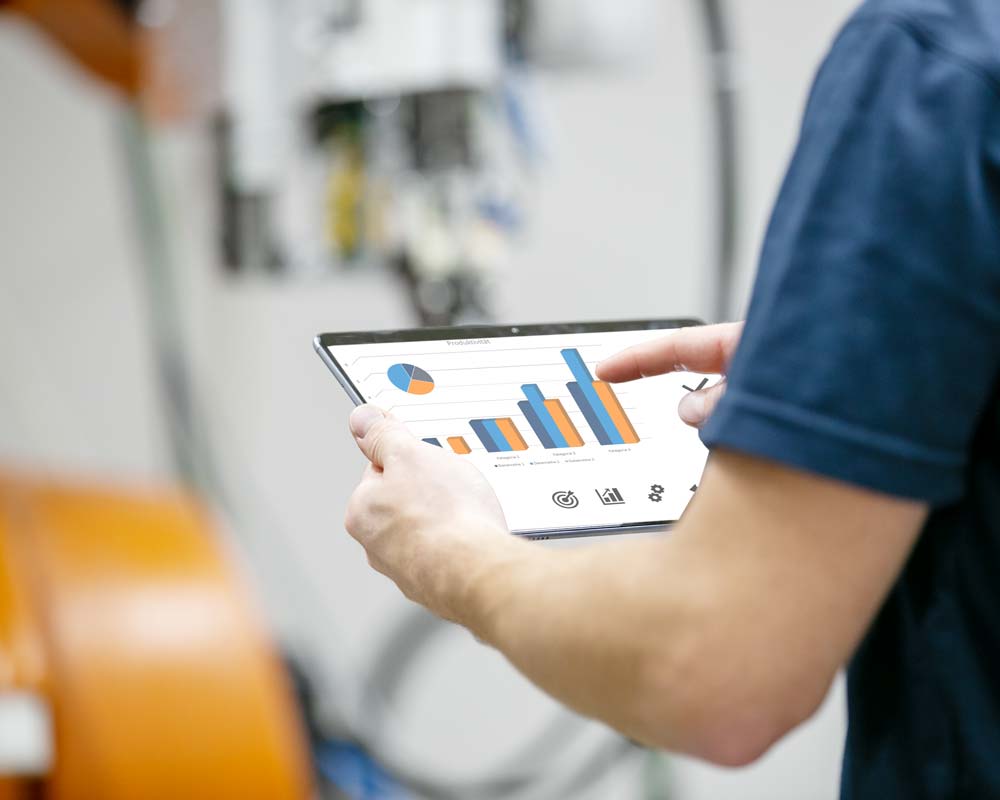
In the event of production downtime, modern companies can now share production information much faster in real time and react accordingly. In the end, Industry 4.0 also allows for better management of the companies in a Group that operates all over the world. WEBER also offers all standard interfaces that can be integrated with our customers’ systems. For screw connections, we record the results of the connections and torque curves and transfer them to in-house manufacturing execution systems (MES). All data are therefore always accessible through standardised interfaces. This system also allows for local statistics functions. Our customers can use their own tools to carry out global analyses. This allows for speedy detection of anomalies in the production process and the corresponding reactions. In addition to this, other statistical functions and evaluations are possible through artificial intelligence. This offers a crucial advantage in particular for screwdriving and feeding systems in the automotive industry. Subsequent verification of screw connections avoids recalls – and saves money. In addition to this, the networking of devices generally increases productivity. Problems are detected immediately and eliminated quickly.
What is so revolutionary about Industry 4.0?
Industry 4.0 is revolutionary because of the optimised self-organisation of companies. The digital development promotes better cooperation between machines and between humans and machines. But it is not only optimised communication strategies that play a role here. In light of the increasing global interconnection, companies now have attractive opportunities of improving their value chain, making their production flexible and customising their products and services.
How current business models for screwdriving and feeding systems are changing with Industry 4.0
Business models in connection with screwdriving and feeding systems are changing with Industry 4.0 because more services are available for the product. Remote services, for example, can be used by engineers to work remotely and carry out programming changes off-site. Electronic QR codes offer customers worldwide easy access to descriptions of machine commissioning, detailed documentation or services. Additional software functions can easily be ordered for data-driven business models.
How companies can save Industry 4.0
It is much easier today for modern companies to avoid product recalls, which saves time as well as money. How does that work? For automatic screw connections, for example, all data are recorded and checked in random samples. The error rate is reduced towards zero with continuous (including retroactive) re-testing. For automotive customers, it is possible that a supposed OK curve shows minimal deviations which will be identified as false OK results with continuous digital checks very early on. This avoids grinding in rework. Of course, money has to be invested in digital applications initially. In the medium to long term, however, this investment will definitely pay off for companies with complex, worldwide operations. So-called “digital twins” now make it possible to visualise all prototypes perfectly on digital platforms. This means that advance simulations can be used to save time during commissioning and start of production. Detailed information can be found here:
https://www.vdi-nachrichten.com/shop/digitale-schraubentechnik/
Source: VDI 2019 ISBN 978-3-18-092347-5
Implementation Industry 4.0
Industry 4.0 links physically remote production machines, transport systems and storage systems with the corresponding planning and control systems. This interconnection creates interfaces that require a common standard (stage 1). The real-time control of the machines changes daily work processes. Machines are operated not only be employees, but humans and machines collaborate actively (stage 2). All this results in cost-efficient production. It also allows manufacturers of screwdriving and feeding systems to better address customer requirements (stage 3). Each stage is the prerequisite for the next.
Here is an overview of all 3 stages.
Stage 1: Cyber-physical system (CPS)
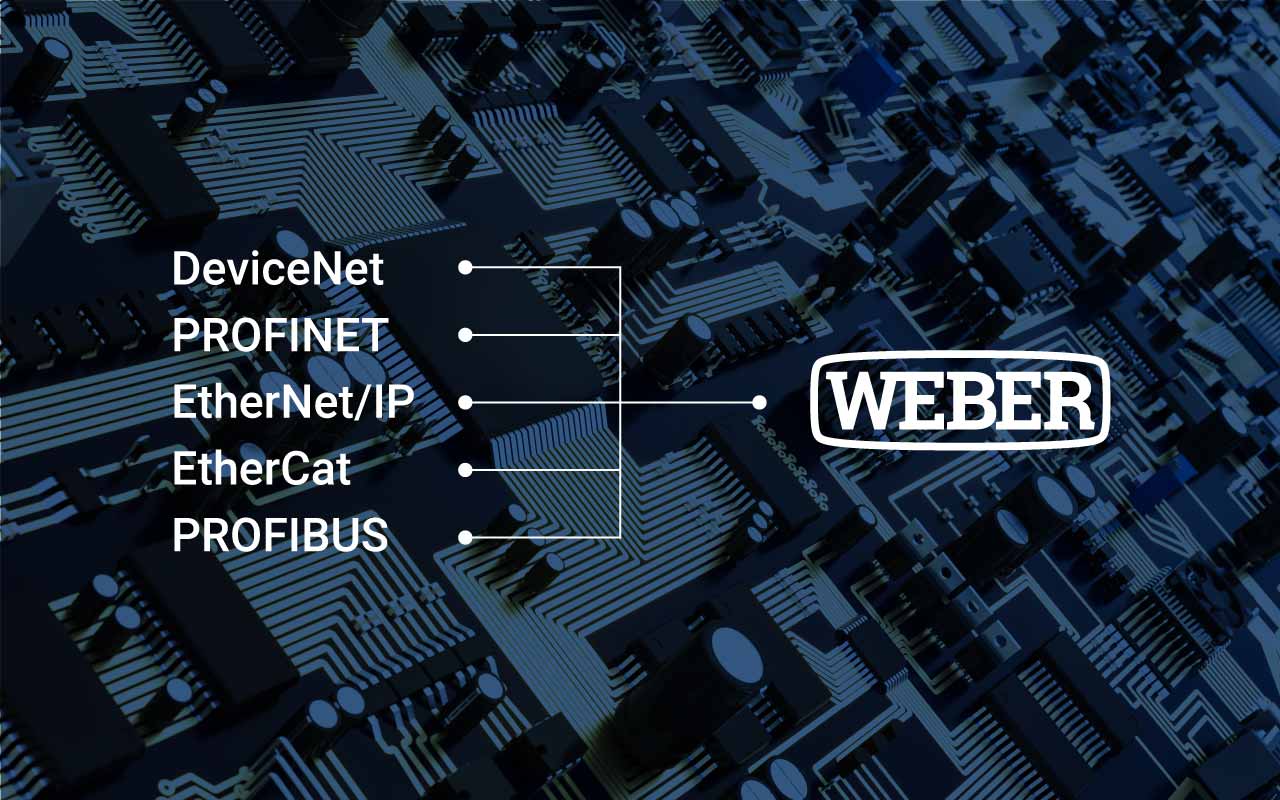
- Ubiquitous computing: Information processing with embedded hardware and software, intelligent production equipment, products and machines
- Standardised interfaces
- Internet of things and services: Linked over the Internet (IPv6), provision of services over the Internet
- Cloud Computing: Big Data Analysis, Bereitstellung of IT-Resource
- Cyber Security required
Stage 2: Cyber-physical production system (CPPS)
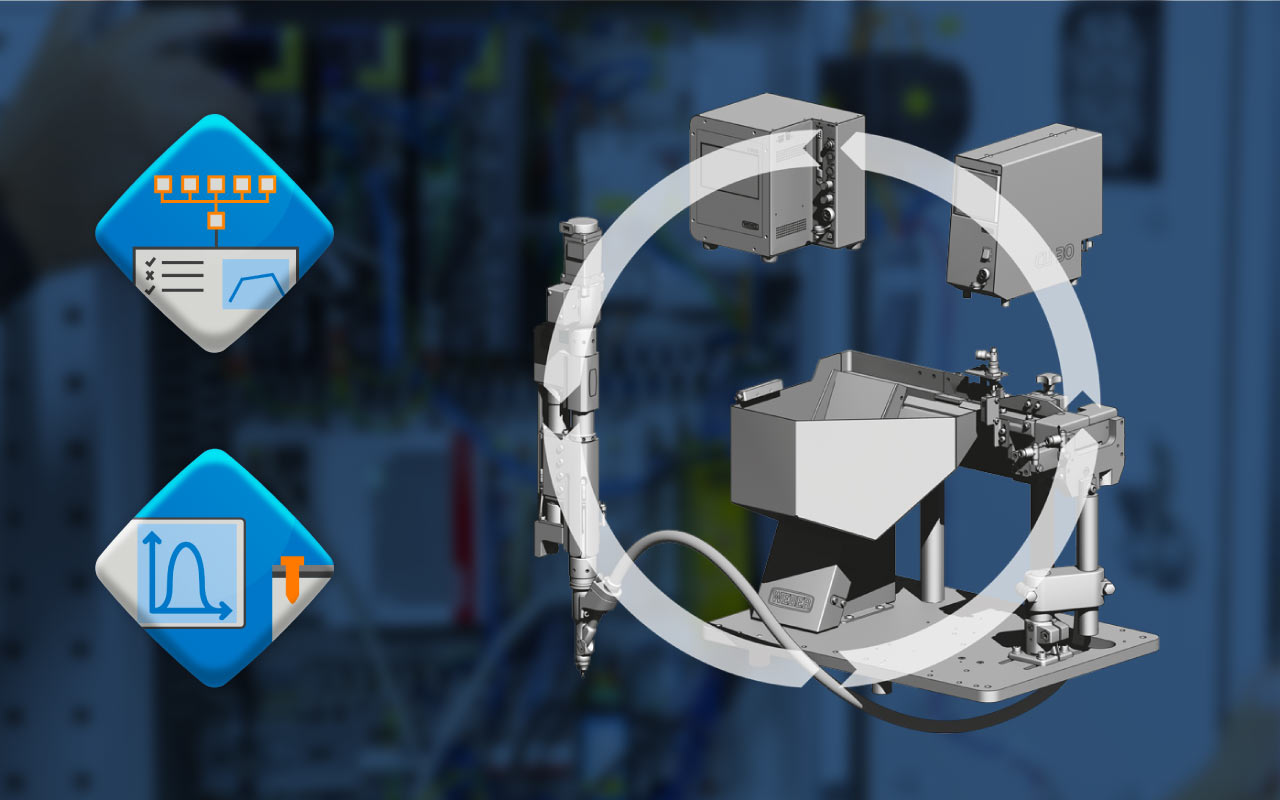
- Machine-to-machine communication: partially autonomous control
- Human-machine interaction, e.g. virtual reality
- Automated data transmission to MES systems
- Big data analysis (using artificial intelligence)
Stage 3: Industry 4.0
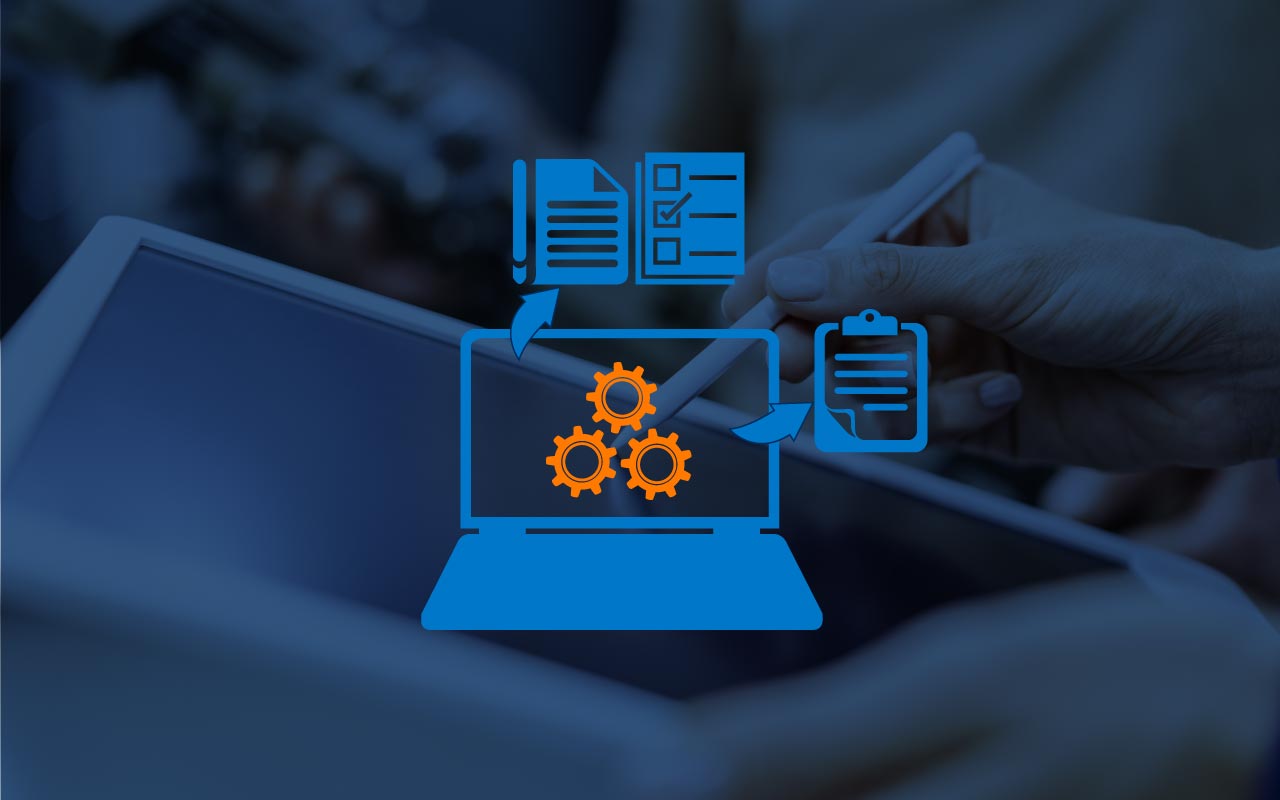
- New company visions
- Strategy adaptation
- New business models and processes
Bottom line: Opportunities with Industry 4.0 – Overview
In summary, the development of Industry 4.0 offers extensive opportunities, in particular for manufacturers with a high standard of automation:
- Automatic data evaluation
- Faster action times
- Higher economic efficiency
- Better production flexibility
- Control across companies
- Location-independent
- Saving resources and energy
About our expert!
Nora Erdei has been working as a product manager at WEBER Schraubautomaten GmbH for 2 years. She specializes in the product range of screwdriving spindles and the digitalization of screwdriving curve analysis. After studying Industrial Design Engineering, she designed the spindles she is now responsible for. Thanks to her Master of Science degree in industrial engineering, she also has the necessary know-how to successfully combine technical and economic aspects.
WEBER Schraubautomaten
WEBER Schraubautomaten GmbH is a family-run and innovative company that attaches great importance to the sustainable design of the value chain. The result is high-quality products with maximum process reliability that make production processes more efficient. Your success is our success.