Are you interested in our previous projects in the field of screwdriving technology for aviation? Here, you can get an overview through selected examples.
Screwdriving technology for aviation industry
Advantages of Screwdriving Technology for Aviation
Efficiency Increase through Cycle Time Optimization
WEBER screwdriving systems significantly enhance your efficiency by allowing for short screwdriving times. This automation relieves your staff and ensures faster production processes. Particularly in the aviation industry, efficiency improvement through cycle time optimization is becoming increasingly important.
Precise Process Control and Monitoring
By using modern real-time screwdriving process controls, we enable exact shut-off when the preset torque is reached. This ensures consistent quality of the screw connections.
Adaptable Screwdriving Procedures for Aviation
WEBER offers you customizable screwdriving programs that we can optimize for each of your desired applications. These include torque, rotation angle, screw depth, and screwing speed, tailored to your specific use case.
Technical Cleanliness through Advanced Feeding Technology
Our automatic WEBER feeding technology allows screws and other fasteners to be transported efficiently and cleanly to the screwing points. Additionally, the use of our dirt brakes and vacuum screwdriving technology ensures a high level of technical cleanliness.
Our Examples of Screwdriving Technology in Aviation
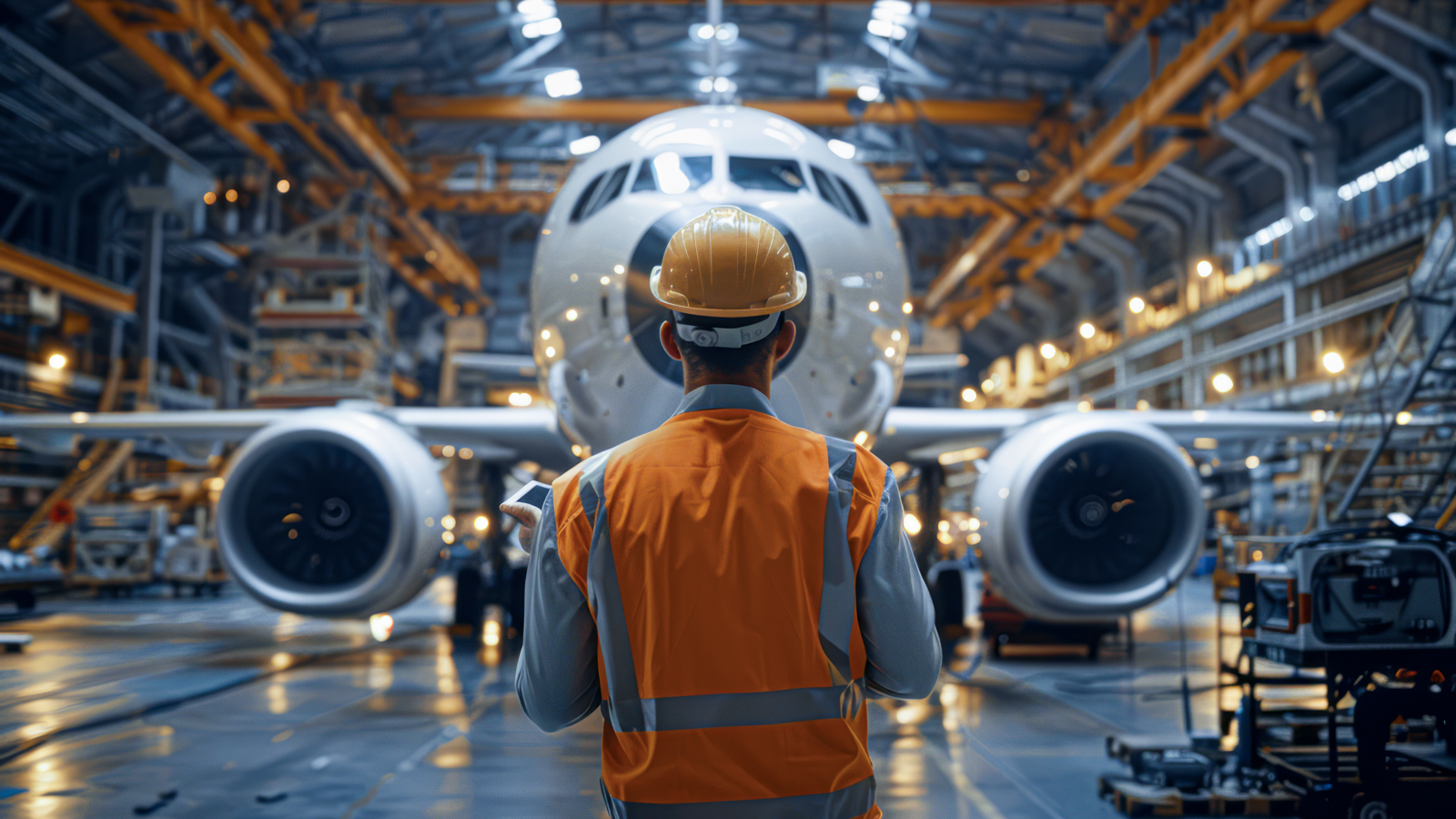
Fitting Rivets: Precision in Aviation
Fitting rivets is a crucial component in aircraft manufacturing, especially in the production of window frames, such as those in the standard series of a well-known European aircraft manufacturer. These rivets are inserted into drilled holes and are designed to sit flush with the surface. The rivets are inserted manually, and the Hi-Lok collar is screwed onto the thread of the fitting rivet from the opposite side. The collar has a hex drive and is equipped with a break-off groove. Once the correct tightening torque or pre-tension is reached, the hex drive breaks off without any intervention from the user. This process requires a high level of precision and care, as the rivets are crucial for the structural integrity of the aircraft. This technique plays a central role in aircraft manufacturing.
Hi-Lok Collar: Manual Perfection
The Hi-Lok collar is a proven fastening technology in aviation, functioning similarly to a nut. In this method, the Hi-Lok collar is tightened until the hexagonal head breaks off, indicating that the required torque has been achieved and the connection is correct. This technology is performed manually and is particularly important when installing fitting rivets, such as the 180 rivets surrounding each window of a typical European single-aisle aircraft. For the reinforcing ribs in the rear fuselage, due to difficult accessibility, we have developed a special hand-setting device with automatic feeding technology to improve the efficiency and accuracy of the process.
Hi-Lok Collar: Easy Access
A renowned Brazilian aircraft manufacturer has also adopted the Hi-Lok collar screwdriving technology. Compared to European aircraft, the accessibility is less complex in these. This simplified accessibility allows for faster installation of Hi-Lok collars, which in turn accelerates the entire production process. The application of this technology in Brazilian aircraft has shown how important tailored solutions for different aircraft types are to ensure optimal assembly conditions for you.
Onboard Kitchens: Lightweight Innovation
In another European aircraft series, there are up to 16 galleys, which are mainly made of aluminum, titanium and lightweight materials due to the need to save weight. These kitchens use honeycomb components, a construction that is also used in the automotive industry for lightweight but stable components.
The thermoplastic screw for thin sheets is an innovative fastening solution specially developed for the efficient and secure connection of thin sheets from 0.5 mm thickness without pre-punching or tapping. This self-forming screw reduces assembly times and costs by offering high pull-out resistance and vibration-resistant connections. The thermoplastic screw is versatile and can be used in various industries such as the automotive industry and electrical engineering, where it enables durable and reliable fastening. Their unique geometry and special thread profile ensure low screw-in resistance and optimum power transmission.
Our Video: Screwdriving Technology for Aviation
You are currently viewing a placeholder content from YouTube. To access the actual content, click the button below. Please note that doing so will share data with third-party providers.
More InformationWEBER is your expert for state-of-the-art screwdriving technology in the aviation sector. Our solutions are tailored for engineers and specialists in aircraft equipment and interiors. Whether it’s the assembly of aircraft structures or the installation of onboard kitchens, our innovative screwdriving systems ensure the highest precision and reliability.
Discover the Future of Aircraft Assembly.
Do you have questions about screwdriving technology in aviation?
Frequently Asked Questions about Screwdriving Technology in Aviation
What information do we receive about the screwing processes?
You will receive detailed documentation on the screwing processes, including three key parameters: torque, screw-in depth, and rotation angle. These precise data are crucial for quality controls and assurances, particularly in industries such as aerospace, automotive, and medical, where warranties, guarantees, and product liabilities require accurate documentation of assembly processes.
How long do the screwing processes for aerospace take?
We have optimized the cycle times of our screwing processes with the WEBER swivel arm principle. We ensure efficient and timely assembly, with the exact duration depending on the number of screws and machines used.
How long can the feeding device operate without needing to be refilled?
WEBER has developed systems that enable longer autonomy. For example, a bulk resupply hopper extends autonomy by automatically dropping new parts into the feeder as it runs empty. This conserves personnel resources and increases the efficiency of your assembly process.
Can your systems reach hard-to-access areas in and on aircraft?
Yes, WEBER technology enables access to hard-to-reach areas. The vacuum screwdriving technology is particularly advantageous here, as it uses a suction tube to create a vacuum that places screws precisely in the right (even hard-to-access) spots. Additionally, with the help of special hand-held devices, we ensure precise and secure fastening in challenging assembly areas.
More Applications
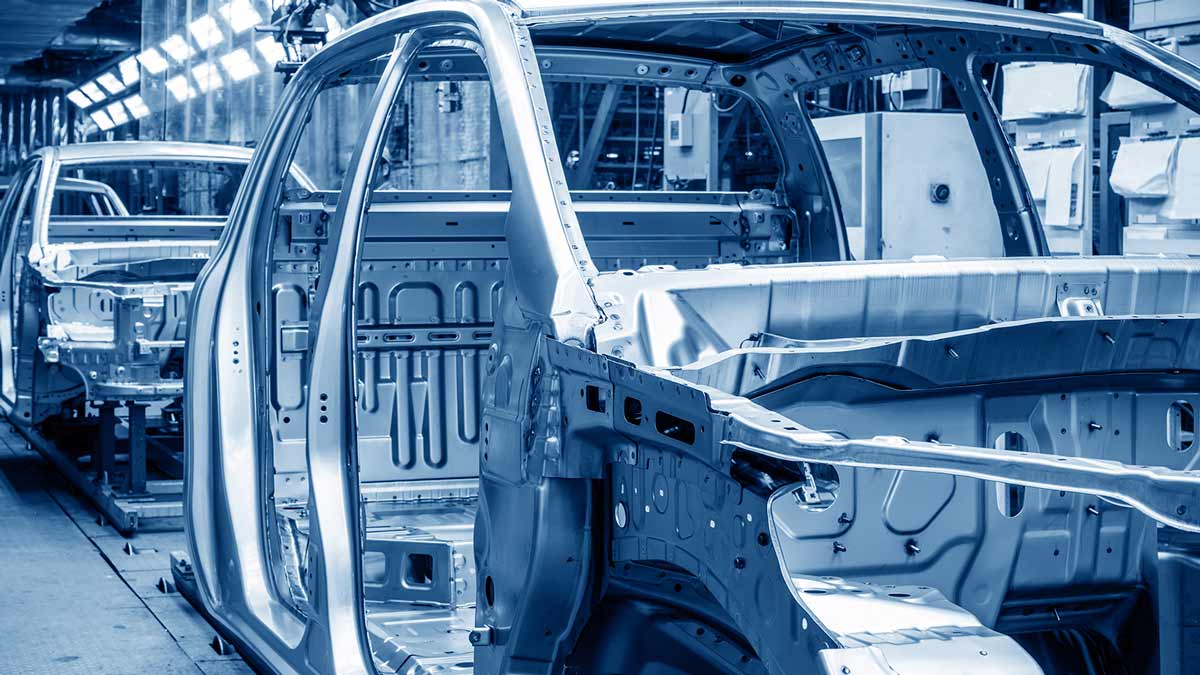
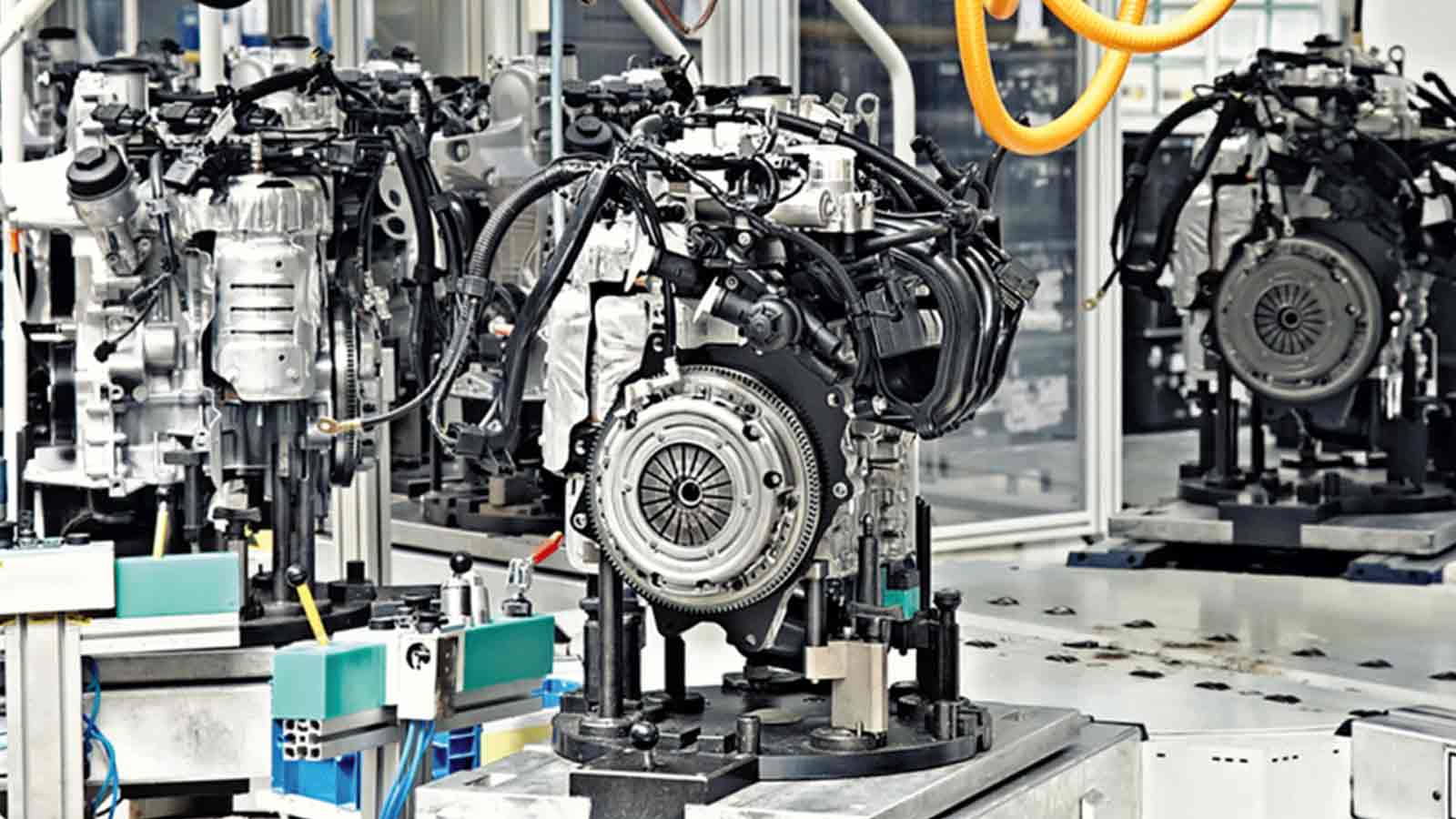
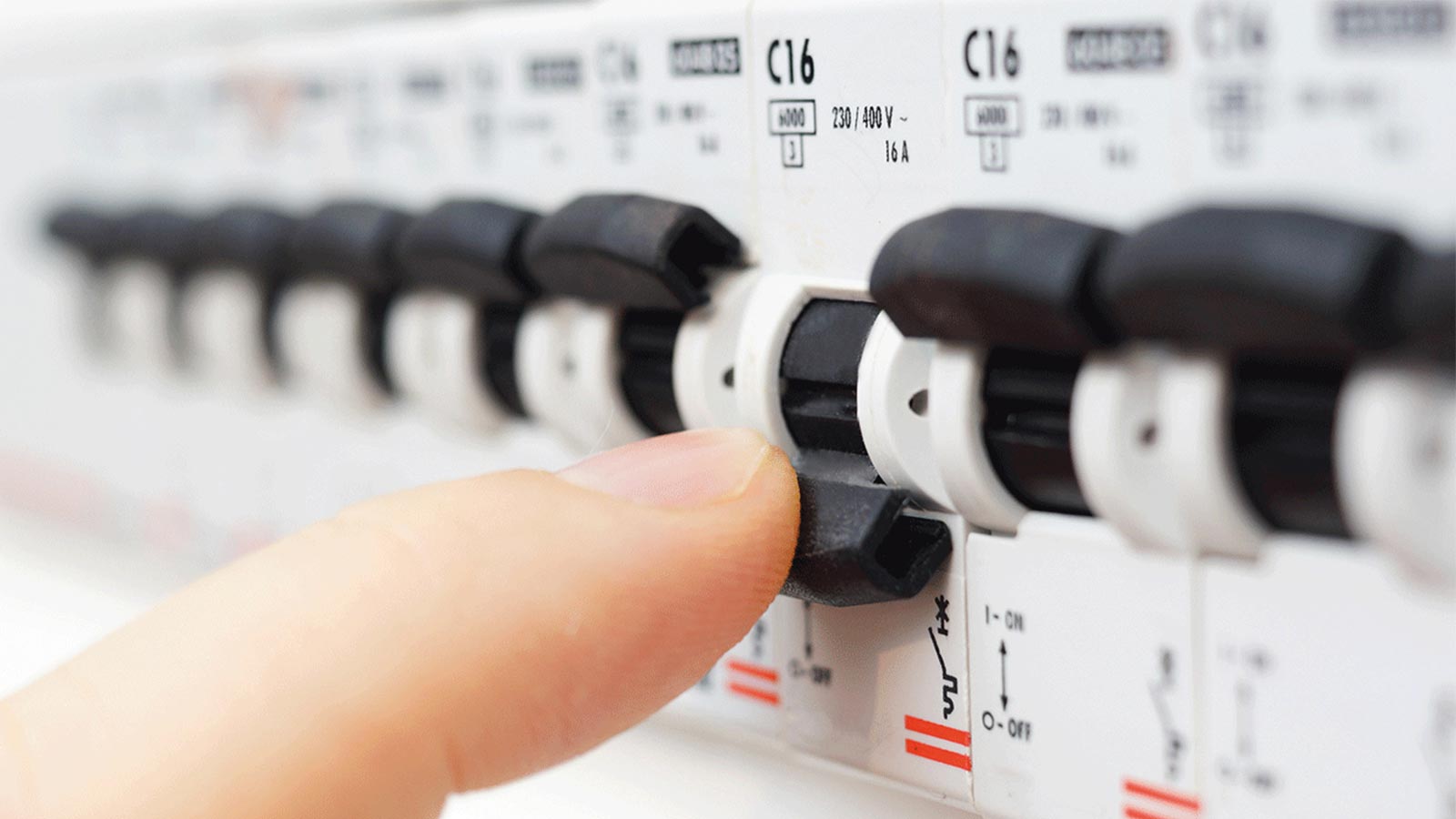
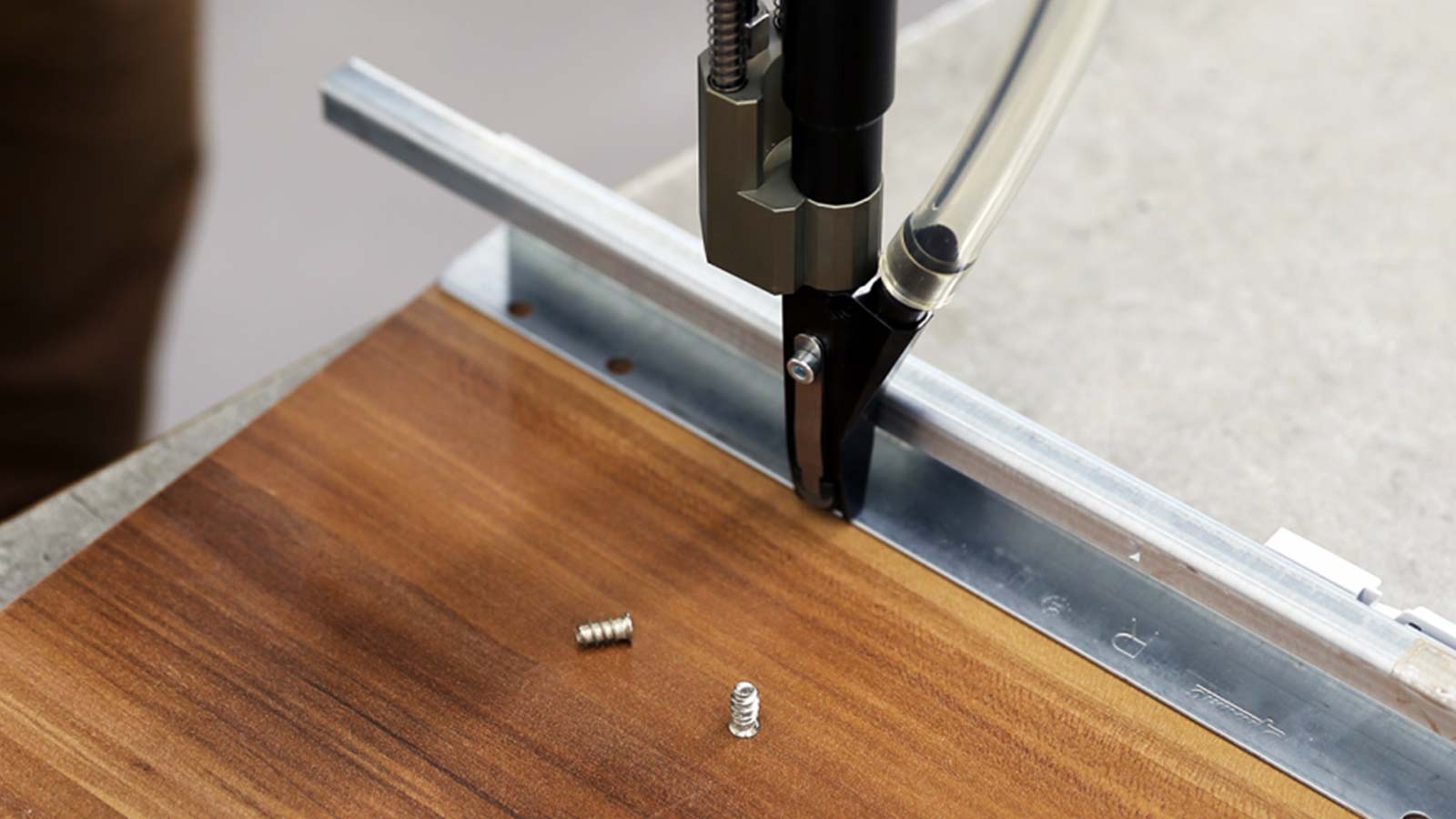
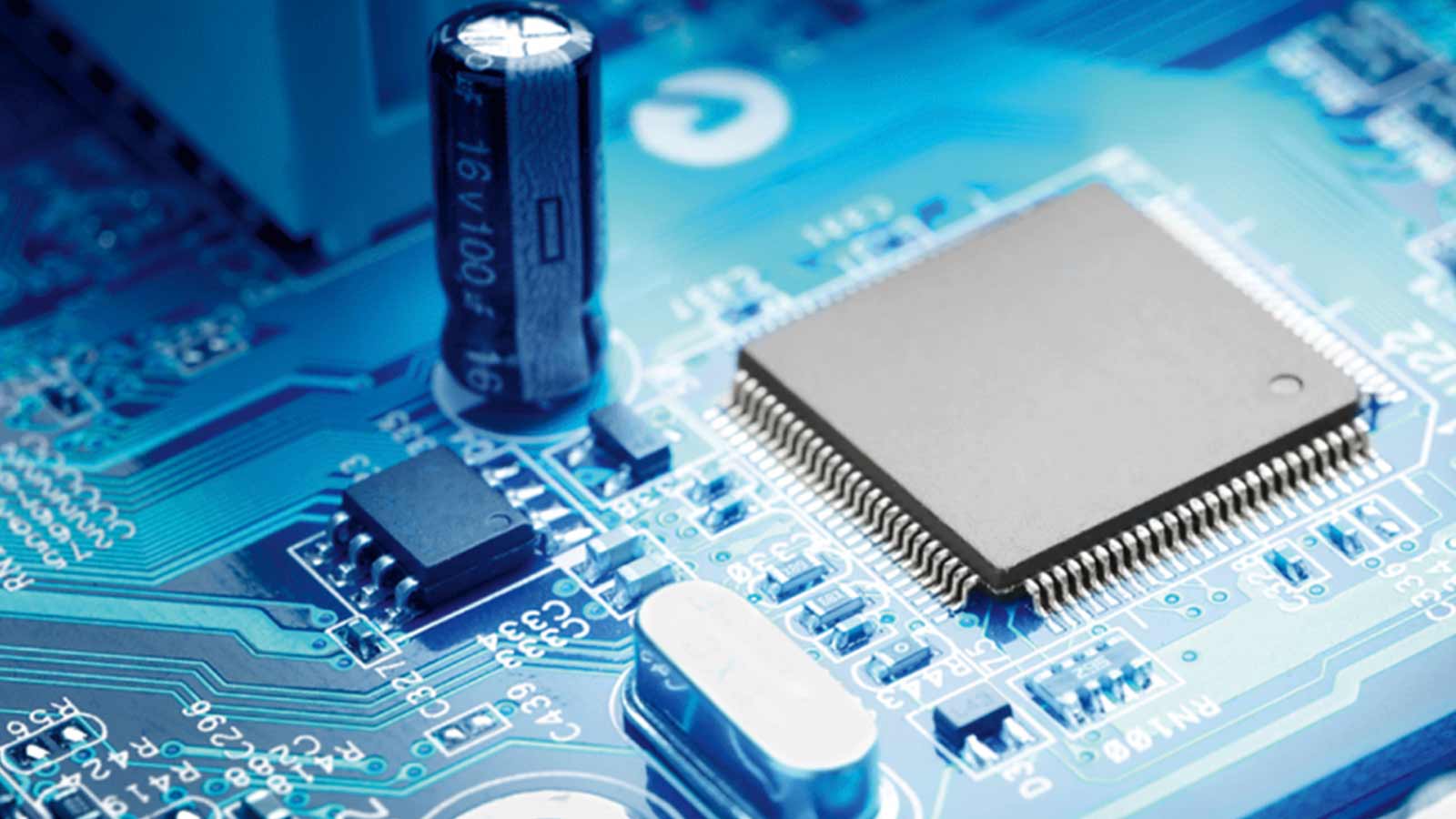
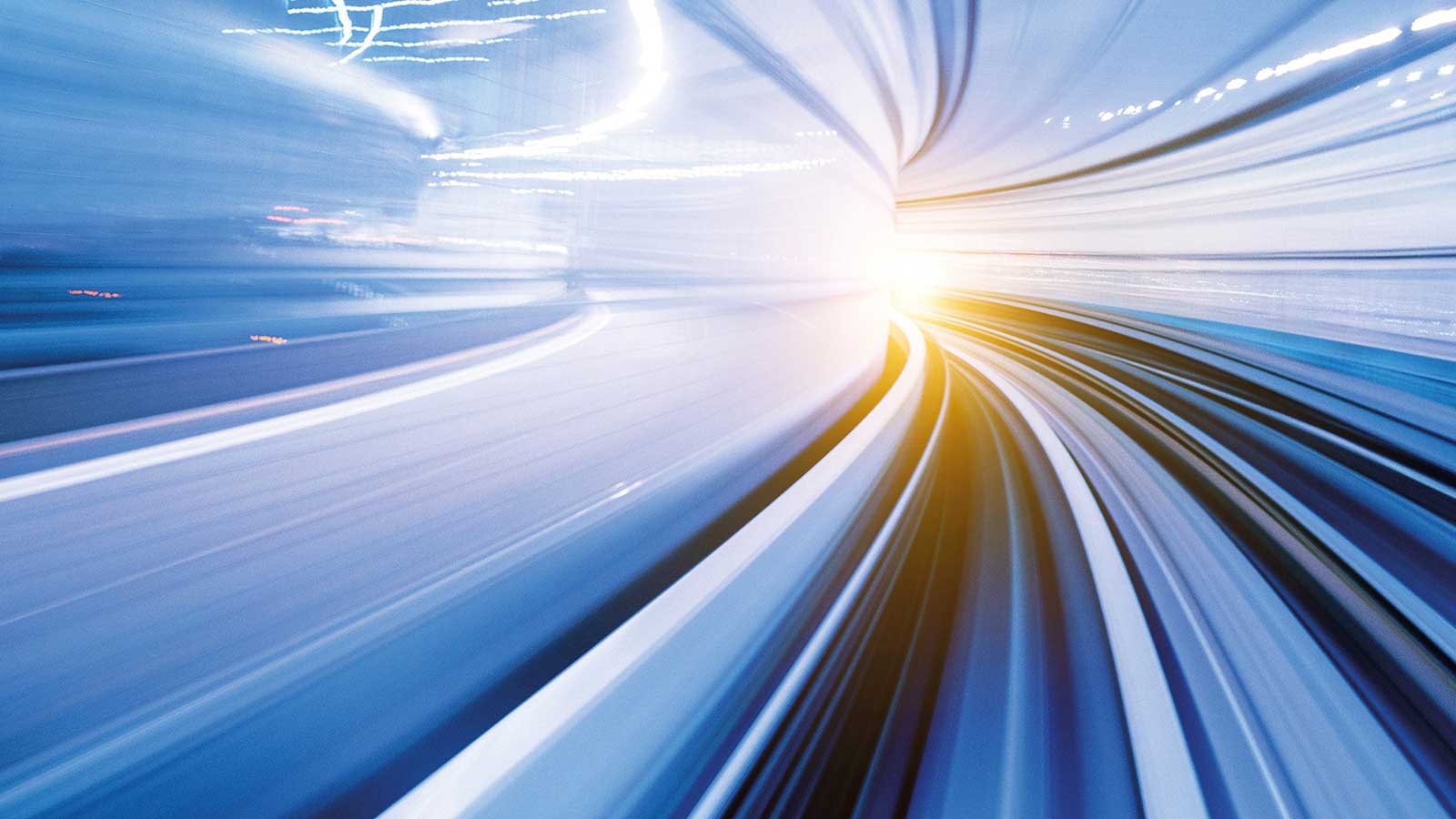
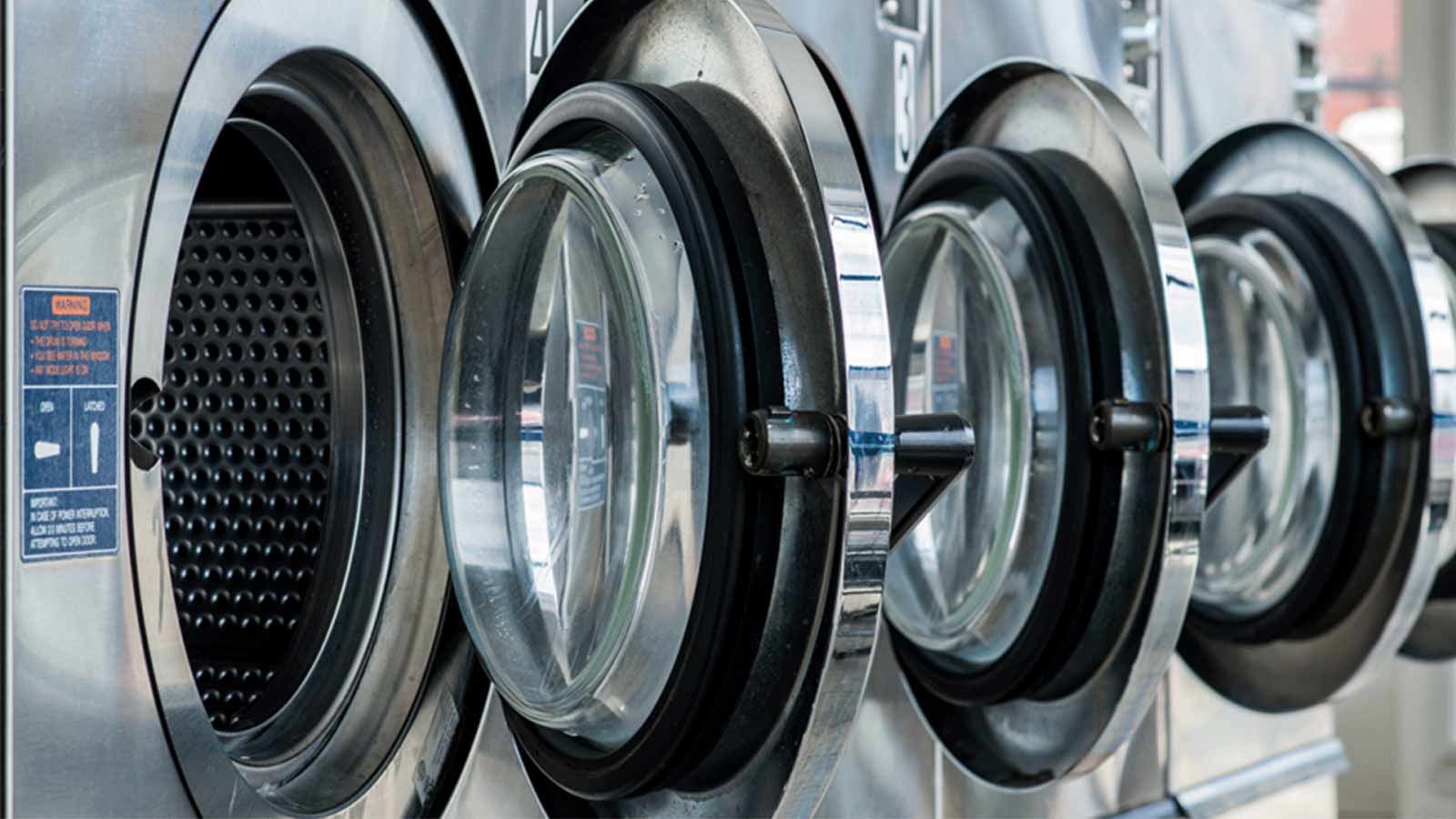
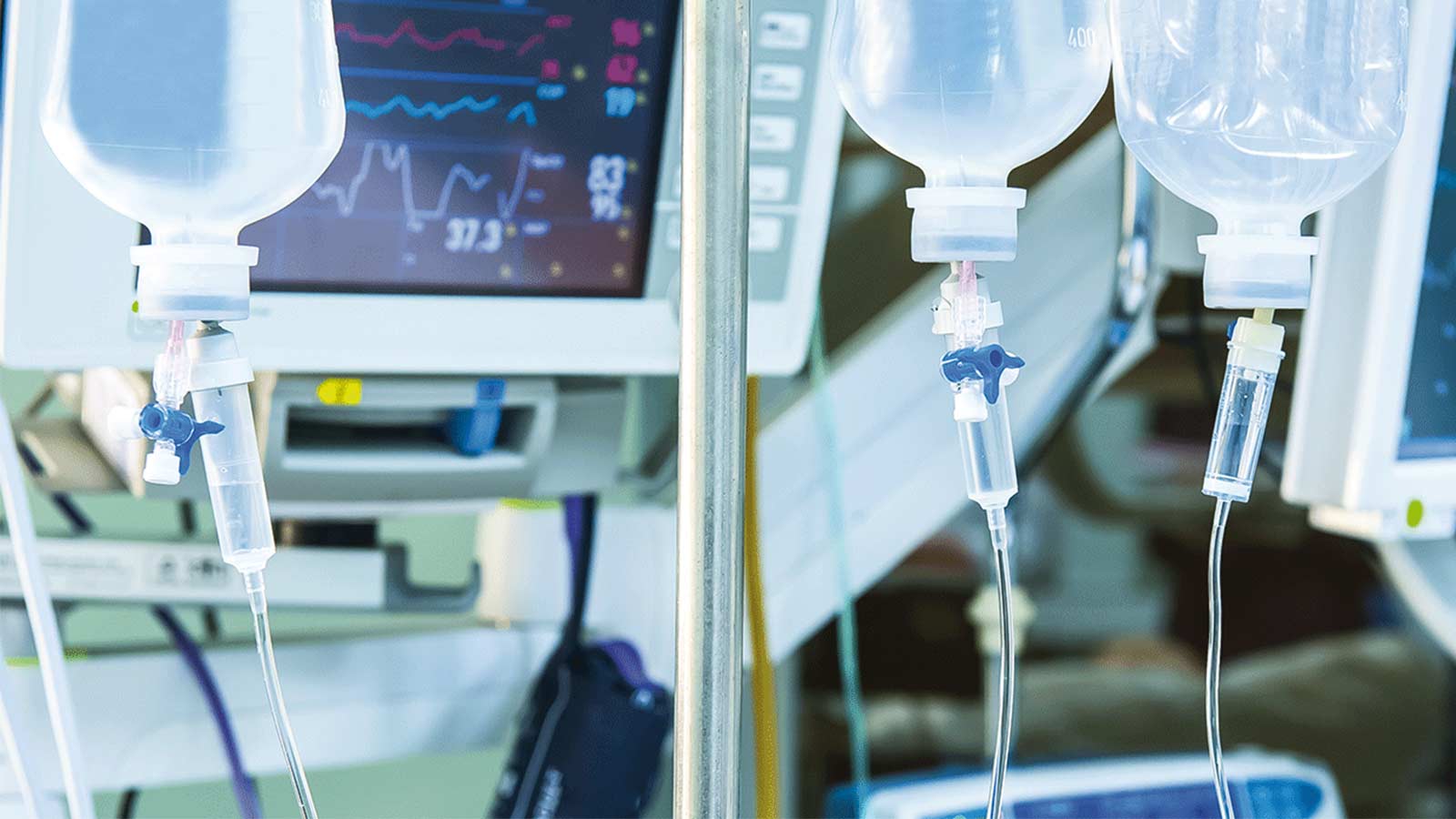
WEBER Schraubautomaten
WEBER Schraubautomaten GmbH is a family-run and innovative company that attaches great importance to the sustainable design of the value chain. The result is high-quality products with maximum process reliability that make production processes more efficient. Your success is our success.