To optimize your assembly processes, you have the option to use our automated screwdriving technology in your manufacturing processes with robot applications. Here, you will learn everything you need to know about integrating our screwdriving technology with your systems. Hier erfahren Sie alles, was Sie über die Zusammenführung unserer Schraubtechnik mit Ihren Systemen wissen müssen.
How to Use Automated Screwdriving Technology in Manufacturing Processes with Robot Applications
How Our Screwdriving Technology Integrates into Your System
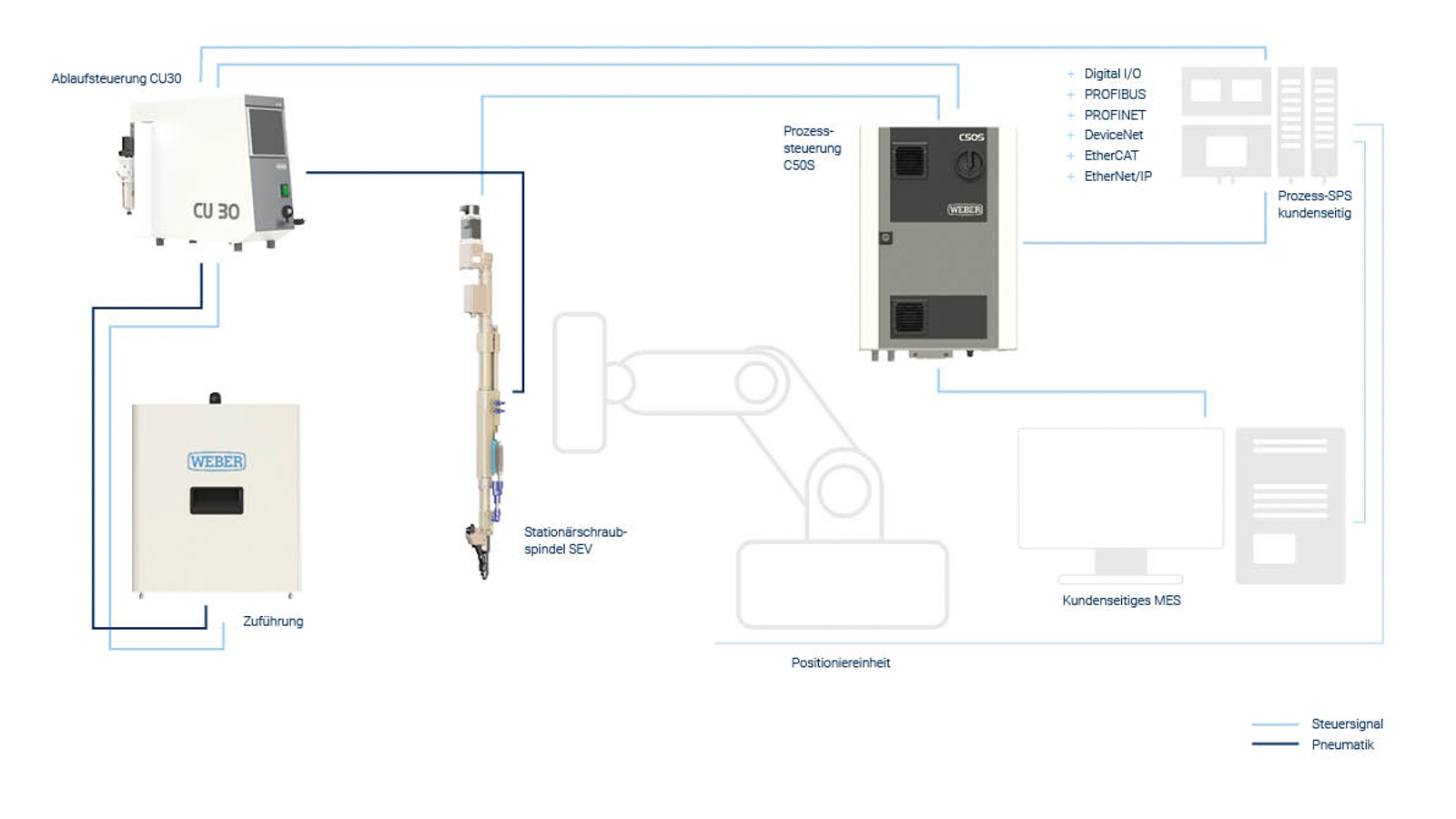
Our screwdriving technology can be easily integrated into your system. For your robot applications, we offer our screwdriving spindle, feeder, and control system. Our assembly systems can be integrated into both simple and complex robot installations with minimal effort. We use our compact screwdriving spindles to avoid any interference contours. Additionally, these spindles are very lightweight to avoid exceeding the load capacity of your robot. At WEBER, you will receive an electrical and pneumatic functional plan for integrating our screwdriving technology into your robot application. It is based on the communication interfaces you specified in advance. While most screwdriving technology providers work with open housings, we use closed housings for our products to protect them from damage and dirt accumulation. This is how you integrate our station screwdrivers into your production:
Good to know
WEBER screwdriving spindles operate in all directions.
Our screwdriving systems can also screw “overhead” and prevent the screws from falling back.
Pay attention to the load capacity of the robot when integrating our screwdriving technology.
Robot-Compatible Cables and Hoses
For multi-axis movements and additional loads in your robot applications, we offer the use of robot-compatible cables and hoses. Robot-compatible cables must withstand millions of cycles as well as the stresses from tension and torsion. Therefore, cables for robot applications are absolutely torsion-resistant, temperature-resistant, and resistant to oil or chemicals. The Weber range includes both robot-compatible and drag chain-compatible cables. In the area of feeder hoses, we offer different solutions depending on the application. By default, polyamide hose is used for transporting the screw. It is characterized by hardness and high pressure resistance, good resistance to chemicals, oils, and fuels. The PUR hose (polyurethane) is characterized by high flexibility, elasticity, and abrasion resistance, making it particularly suitable for frequent twisting and bending, and good resistance to oils and fats. For OEM products, we offer a double-walled hose, a combination of both materials. Thus, the best properties of both hoses are combined: Abrasion-resistant inside (for pointed screws), hard and durable, outside resistant for frequent twisting and bending.
- PA Hose (Polyamide):
characterized by hardness and high pressure resistance, especially designed for dynamic movements and high mechanical loads, good resistance to chemicals, oils, and fuels. - PUR Hose (Polyurethane):
characterized by high flexibility, elasticity, and abrasion resistance, especially suitable for frequent twisting and bending, good resistance to oils, fats, chemicals, and UV radiation. - Combination of PA Hose and PUR Hose
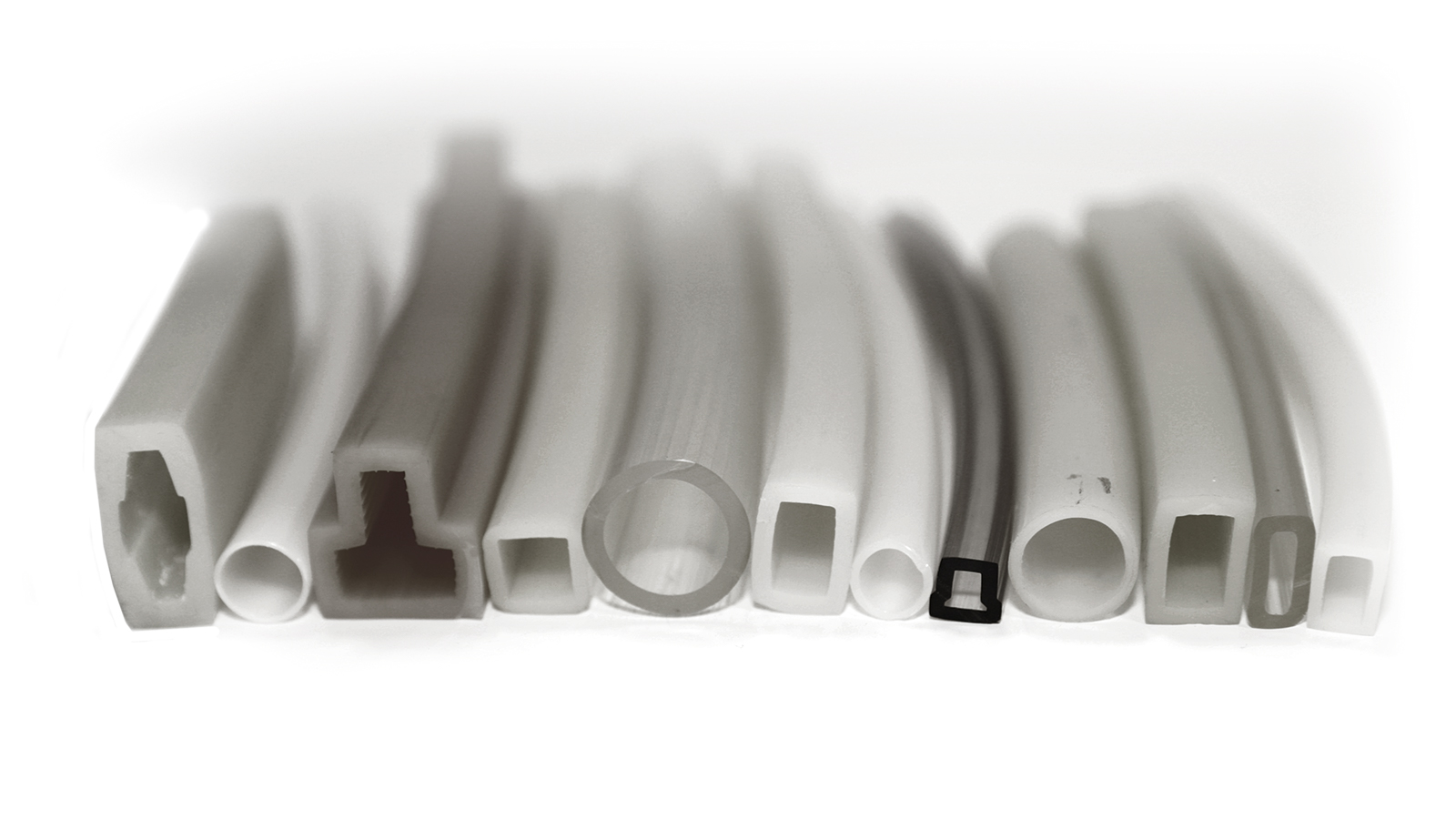
How to Attach the Screwdriving Spindle to the Robot
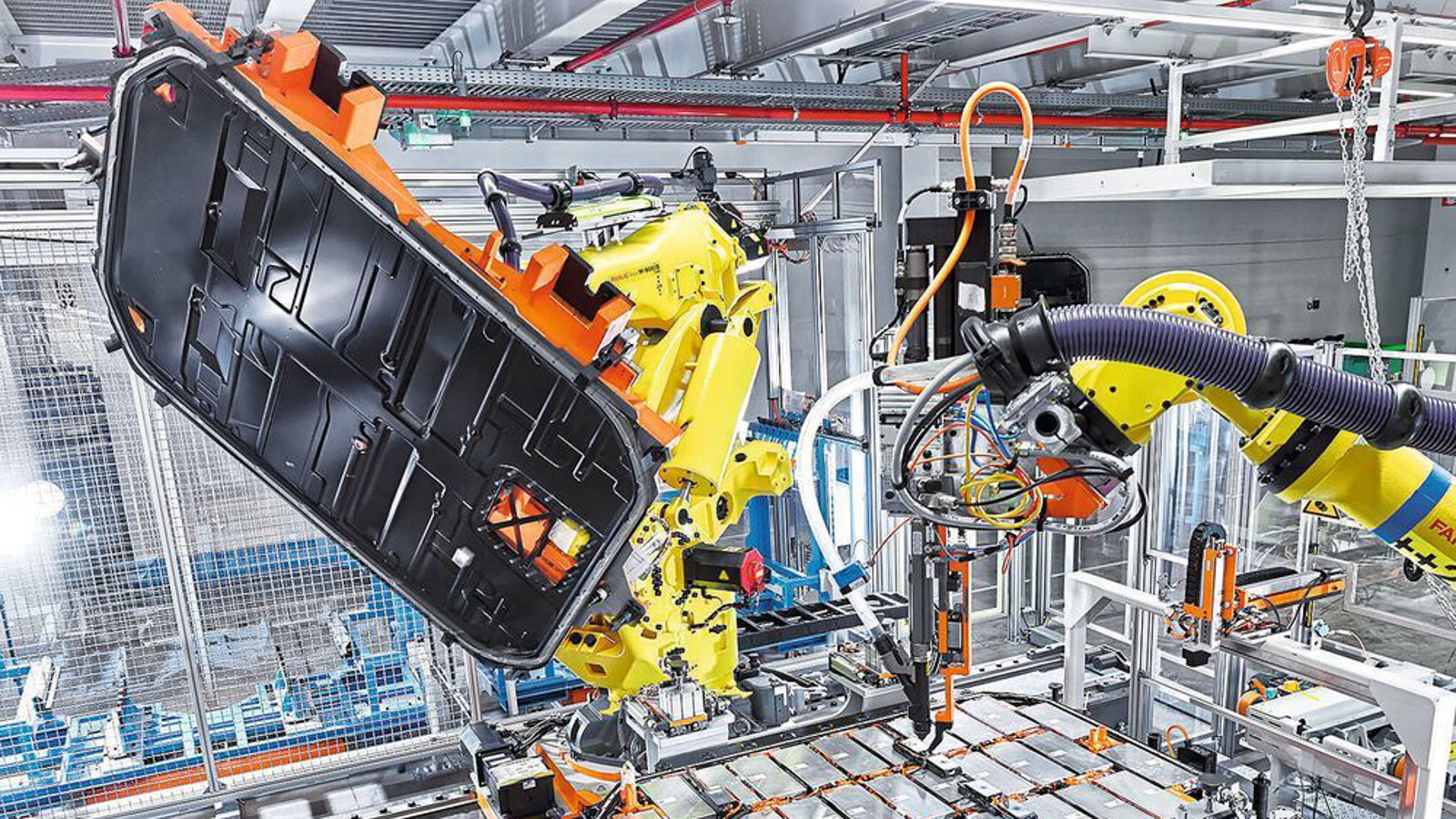
Attaching a screwdriving spindle to a robot is crucial for the efficiency and precision of your production. To ensure a suitable attachment solution, it is important that you specify the exact type of your robot. Depending on the robot manufacturer, the hole patterns can vary, and so can the specific requirements for attachment. Depending on the screwdriving configuration used and the type of robot, there are three main methods of attachment:
- Mounting Bar for Standard Stationary Screwdrivers:
Our standard stationary screwdriver models (SER, SEB, SEM, SEK, SEV, SEV-E) can be easily and securely attached with a mounting bar. This method is particularly suitable for fixed applications. - Standard Robot Flange for Lightweight Spindles:
The lightweight spindles (SER-L, SEV-C, SEV-P) are equipped with a standard robot flange according to ISO 9409-1. This standard allows for uncomplicated and quick attachment to most common robot models. - Dockable Robot Flange:
Our OEM products offer additional flexibility through their docking capability.
With these attachment options, we ensure that your screwdriving spindle is securely and efficiently mounted on your robot.
On request, we also manufacture special flanges or special mounting plates that are specifically tailored to your requirements.
Screwdriving Technology with Safety Devices
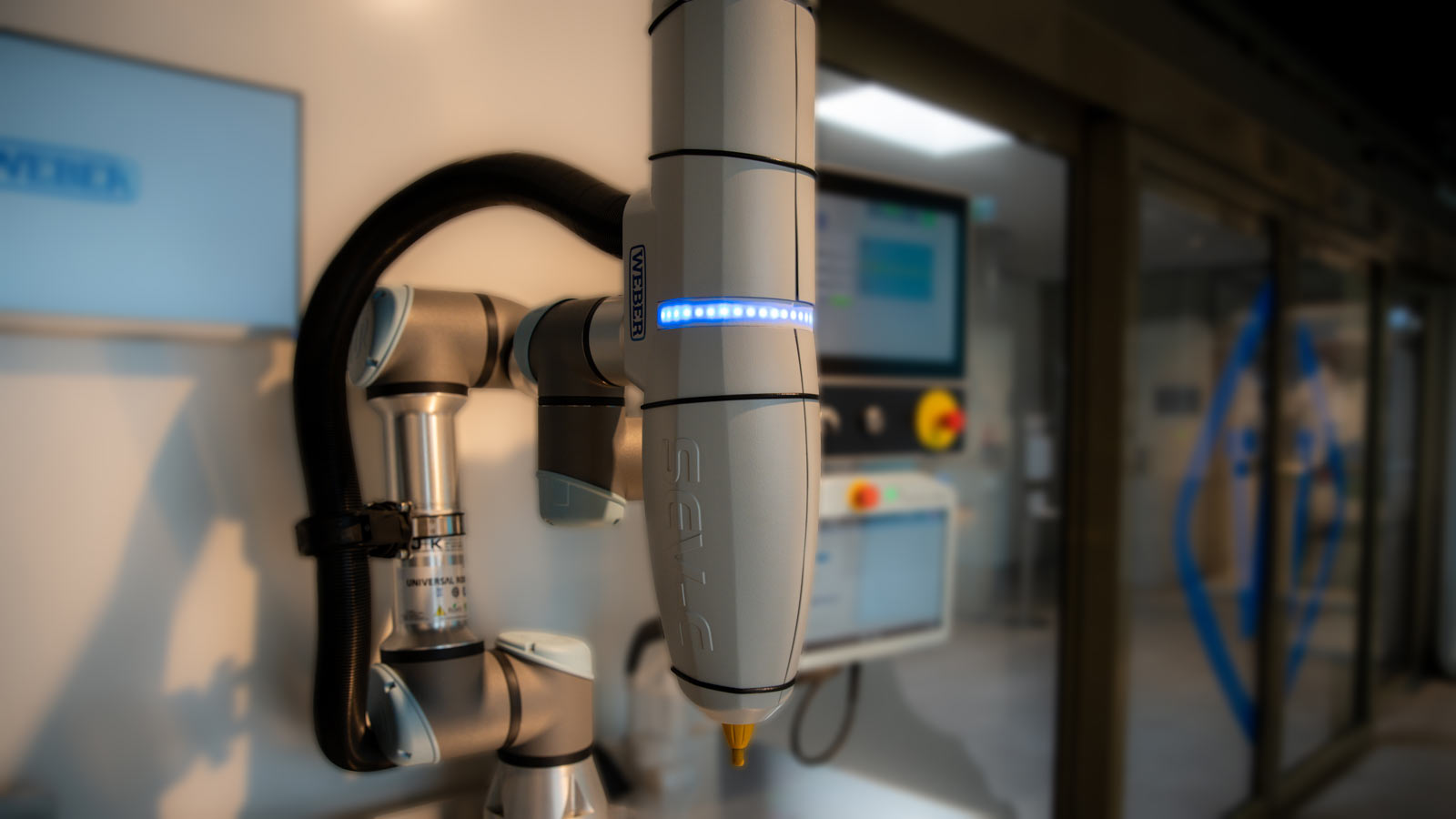
To integrate screwdriving technology into your robot application, you are required to implement safety fences, emergency door openings, and all other safety precautions according to current standards. Our MRK screwdriver SEV-C already has an integrated safety device for fully collaborative screwdriving. This provides you with the best safety concept for fence-free and complex collaboration between humans and robots. We are happy to advise you on its use.
Bottom line
Considering AI-based camera systems and innovative disassemblies, the integration of our screwdriving technology in your robot application is of increased importance. It is indispensable for intelligent solutions for assembly and disassembly. By integrating our WEBER screwdriving technology into your robot application, we offer an intelligent handling of highly effective precision assembly processes. We integrate the entire range of WEBER screwdriving spindles into both simple and complex robot systems.
To our experts
WEBER Schraubautomaten
WEBER Schraubautomaten GmbH is a family-run and innovative company that attaches great importance to the sustainable design of the value chain. The result is high-quality products with maximum process reliability that make production processes more efficient. Your success is our success.